Live from Super Bowl LIII: NFL Media Expands Presence; Bexel Tapped To Build 25,000 Square Foot Facility (repost from SVG)
Excerpt. Article originally published on SportsVideo.org.January 31, 2019 - It has been a busy week for NFL Media in both Atlanta, where Super Bowl LIII will be played this weekend, and Culver City, CA. In Atlanta, a team of more than 400 is covering every angle ahead of the game and working closely with a team of more than 250 people at NFL Media’s facilities in Culver City, where three control rooms have been producing all the coverage for programming from Tuesday to Saturday. And new this year, a fourth control room will be fired up on Sunday for the big game.For the NFL team, each year provides its own set of challenges and opportunities because each host city is unique. Atlanta has arguably provided the most compact Super Bowl footprint in quite some time.“I can’t be prouder of our team,” says Dave Shaw, VP, production, NFL Media. “We developed a plan taking advantage of the unique, centrally located venues in Atlanta, with Opening Night at State Farm Arena, Super Bowl Live at Centennial Park, Super Bowl Experience at the Georgia World Congress Center, and Media Center at GWCC, all in close proximity to Mercedes-Benz Stadium.”The close proximity gave Shaw and the team a chance to build a 25,000-sq.-ft. production hub within the GWCC. Bexel was tapped to supply and engineer a prebuilt system customized for NFL Media’s engineering core, transmission hub, and control room. The only standalone production is NFL Honors, with Game Creek’s Nitro supporting NFL Media’s coverage of the red-carpet show.
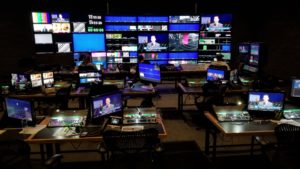
The team in Culver City is working closely with the team in Atlanta and makes sure the intercom system (a massive RTS Adam intercom with 880 ports) and all other signals get to the right location. When nasty weather hit Atlanta on Tuesday and production plans had to be adjusted for programs set to shoot in Centennial Park, for example, ensuring communication between the team in Culver City and the one in Atlanta was critical.This is the third year the team at the game has made use of the at-home approach to produce content. But it’s the first year that Bexel is involved, providing the equipment, integration, and technical support to keep the production-control room, audio area, EVS replay-playback area, and graphics area are online and operating properly.Shaw and the team put the contract for technical facilities out to bid this year, and part of the process included having the finalists construct a dummy of the facility in Los Angeles. That gave the NFL production and operations team a chance to see what the facility would look like and also make adjustments, such as adding a path down the middle of the production-control room, which will seat 15 people on Super Bowl Sunday.Because Bexel is now part of NEP Group, its team was able to leverage the rest of the NEP team.“NEP has matured very well as a company, and their engineering teams are talking to each other,” says Shaw. “They do a lot of flypacks and events like this, and they have a good reputation. They’ve done an amazing job. I felt secure because the NEP engineering team see the big picture, and that helped us in decision-making.”Working and planning the remote-engineering detailed plan with Bexel’s team was NFL Media Technical Manager Kevin Reilly, who worked on every detail with Bexel VP, Technical Services, Johnny Pastor, and NEP UK Technical Manager Richard Lancaster. NFL Media, VP, Engineering, Bruce Goldfeder helped oversee the engineering plan and coordination from the Culver City side of this intricate plan, which incorporates remote feeds to three control rooms, along with Team Cam (Azzurro), TVU bonded-cellular signals, file transfer, and intercom and tally swings.
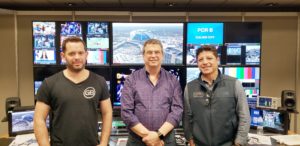
For Bexel, it was a cross-Atlantic effort, with the NEP UK team the playing a role in providing the furniture, especially the desks, which Shaw says made a difference: “You can easily see the monitor wall but also the intercom panel. There are a lot of little things and details I like.”The furniture was also much more shipping-friendly, notes Pastor, and much of it was used for Eurosport’s Olympics efforts and for Wimbledon’s new technical facilities, which debuted this past summer.“You can fit five desks in a case the size you need for a monitor,” adds Pastor. “They are very compact as opposed to something that needs a crate for each one.”The large footprint within the World Congress Center ballrooms provides space for 65 pieces of furniture and ample space for technical equipment and the ability to work with a bit more personal space than is typically found in a live-production environment.“Having this footprint makes it a lot easier: you can plan for space,” says Pastor. “There are about 180 monitors just in these ballrooms with 90 multiviewers, 120 KP panels, and 65 pieces of technical furniture.”The technical specs were large as well and have been achieved with the help of a 1,000×1,000 Imagine IP3 router, which Pastor says has 30 multiviewer cards with 48 inputs and six outputs each. There is also a Grass Valley Kayenne production switcher with 9M/E and 128 inputs; a Calrec Apollo audio console with 96 faders alongside a Calrec Artemis 64-fader console; and two Vizrt graphics engines. The at-home–production rooms house two Calrec Apollo consoles with 40 faders.
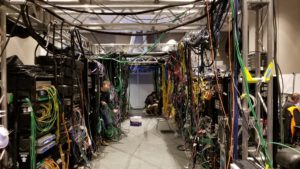
There are also five eight-channel EVS system and two 12-channel EVS servers, as well as 880 intercom ports on three Adam matrixes tied to a fourth in Culver City.“We’ve basically built a TV station that is supporting a network,” notes Reilly.He adds that there are also 528 strands of fiber between the Atlanta sites, including 198 to the stadium and 96 to State Farm Arena.The biggest challenge was simply to have all the production racks and furniture prebuilt and planned so that they could quickly be brought onsite and put together.“We built it exactly the way they wanted it, knowing we would not have much time for changes once we were onsite,” says Pastor. “We wanted to get to the point where we were not reinventing the wheel but rather just making adjustments.”One idea that helped ease operations was to build a truss in the main equipment room. Lancaster had built something similar for Wimbledon, and the truss at the World Congress Center sits between two rows of equipment and allows the cables to pass overhead.“We didn’t want all the cables on the floor,” adds Pastor. “The truss keeps the cables out of the way and makes it easier for us to manage things and get to the back of the racks.”The truss and preplanning enabled the technical team to move in at 5 a.m. on Sunday, get the truss up by 7 a.m., power up by 8 a.m. and have eight trucks of equipment unloaded in one day.“On Sunday, we got the walls up, then first installation on Monday morning, and, by Tuesday, a lot of it was framed,” says Shaw. “We were very impressed.”