August 5, 2016 - Burbank, CA - As many failed contestants can attest, if you can’t stand the heat, get out of “Hell’s Kitchen”. Bexel’s longevity with Fox’s popular reality television show – it has supported the series with equipment and a powerful technical infrastructure since season two – proves it not only withstands the heat but thrives in it.Every year brings new technical and creative challenges to the team at Bexel, as Hell’s Kitchen brings new challenges to it’s contestants. Currently, Bexel furnishes the show with over 70 robotic cameras, up to a dozen ENG cameras, 40 channels of wireless microphones, and full communications systems.
“We go into the facility and install all the technology required to capture the show,” says Rod Allen, Senior Project Manager at Bexel. “With any large reality show, it’s all about the story, and we strive to support that. It’s very important for us to understand all the workflows involved and create a system that enables the creative team to focus on the content.”
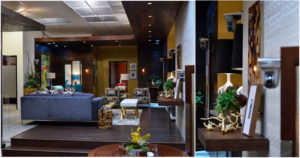
Although “Hell’s Kitchen” is based in a studio production facility, it has a particularly broad scope within those studio walls. The set features two working kitchens, an on-show restaurant and dining room, interview areas, and living spaces for the contestants. To cover that spectrum, the show’s equipment needs typically exceed those of the average reality series. Take more than 70 Panasonic AW-HE60H full-HD integrated robotic cameras, for example – at least twice as many as most reality shows. They’re positioned throughout the facility and controlled by a custom system designed by Bexel engineers specifically for “Hell’s Kitchen.” This enables robotic camera operators to select any of the units from a touchscreen interface. “The software can be deployed for any show but is most useful with large numbers of cameras,” says Allen.Sony PDW-F800 XDCAM cameras
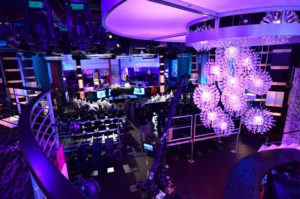
shoot into the living room and kitchens. Up to a dozen of these ENG cameras also travel to location shoots, including outdoor Challenges staged in the parking lot. Cameras record onto Sony PDW-F1600 XCDAM players/recorders, and a large monitor wall in the Main and Executive Control Rooms display all the robotic and ENG camera sources and record decks. If the show’s camera complement is big, so is Bexel’s custom MAS (Managed Antenna System) for Wireless Microphones and IFB. “The MAS for this series is much larger than for most reality shows we do,” says Allen. The show deploys Clear-Com’s FreeSpeak II wireless intercom system, which operates in the 1.9GHz range, opening more spectrum for wireless mics – Sennheiser 5000 Series systems were used for the talent and Lectrosonics SMQV series were used for the wireless camera hops. DirectOut Technologies’ MADI audio distribution system gives access to various points throughout the facility and back via fiber to the hub. “The MADI infrastructure not only allows us accessibility in many areas of the plant but also gives us greater flexibility when there are changes,” Allen explains.
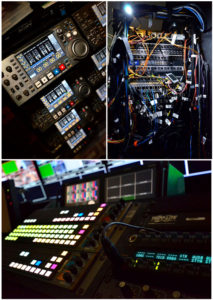
Shows are seldom alike week-to-week, which keeps Bexel on its toes too.
“Half of the show is the Challenge, which may or may not be on site. They could be headed for an outside restaurant or another location,” Allen reports. “At times all they need is a straight forward ENG package, sometimes it may be a small video village, and still other times they may need a control room in a theater with an audio PA package. Once we’ve installed equipment for the season, the job is not over.”
Having supported “Hell’s Kitchen” for 13 seasons and counting, Bexel has developed a very close working relationship with the show’s operational staff. “The technical operations team with the show is incredibly talented,” says Allen. “We love working with them, and we’re here to support whatever they need – helicopter aerials, contestants scuba diving or jumping off buildings. They know they can call us, and we’ll work with them to come up with a way to support what they want to do.”[sc name="news-footer"]